Concept :
The Gulf Stream provides an attractive source to harvest the hydro-kinetic energy of the ocean current. However, the Gulf Stream is not only a busy shipping transportation route, it also nearly 3000m deep at locations where the continental shelf plunges steeply downwards. Fabricating ~3000m tall towers under the sea to support the rotors is an impractical solution. One solution proposed by our joint project group comprising three labs, is to developed a tethered, coaxial, dual rotor, contra-rotating system.
- Why tethered?
Cost effective method to anchor to the sea floor rather than building towers. Since gulf stream current speed is maximum towards the surface (which is also a shipping route), the tethered system can get close to the surface while maintaining high yaw angles to prevent interfering with the ships.
- Why dual rotor?
Tethered system would dynamically change its angle (yaw) with respect to the flow direction as a function of flow speed and multitude of other perturbation/destabilizing parameters. Adding an extra rotor blade could potentially offset the extracted energy loss at extreme skew conditions
- Why coaxial?
Potential cost-savings by utilizing both ends of a single nacelle.
- Why contra-rotating?
To allow for torque cancellation between the upstream and downstream and prevent the tether from tangling up.
Prototype design: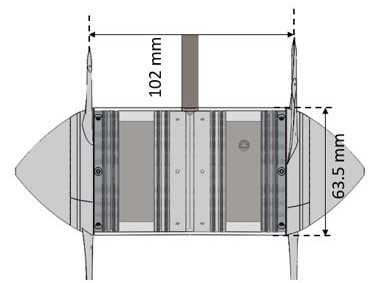
A sting mounted prototype is envisaged that could be tested at prescribed skew angles in a controlled environment - NCSU water tunnel. Most of the parts are rapid prototyped using OBJET 30 3D printer using RGD 835 (Vero White Plus) proprietary material made by Stratasys.
The purpose of the prototype is to measure :
- the mechanical reaction torque (at a given brake resistance) -
- the RPM of the turbine -
This would allow to measure the mechanical energy of the rotor
Special features of the prototype:
- Sealed inner compartment that houses the instruments
- Dedicated instruments for each set of rotors
- Non-contact torque transmission using custom-built magnetic couplers
Instrumentation:
- magnetic hysteresis brake - Magtrol HB-20M
- reaction torque sensor - Futek QTA141
- RPM sensor - KMA 210
Some of the fun stuff that is crammed into a small poly-carbonate body tube!
Data acquisition:
The sting mounted prototype is mounted in the NCSU water tunnel (Dr. Kenneth Granlund's lab)
I designed a custom LabVIEW VI to interface with the instruments and record the data to file. The VI simultaneously records the voltage signals from the 2 RPM sensors and 2 reaction torque sensors.
The GUI interface of the VI is shown below
Preliminary results:
The power drops off nonlinearly with increasing yaw angle until the rotor stalls. The stall angle is reduced when the prototype is loaded to higher resistive torque, (analogous to higher load) results in reaching the stall yaw angle earlier. The small differences in power when observed from yawing right versus left appear to be negligible. These differences are thought to be attributed to the rotor rotation direction, where when yawing left the rotor blade trailing edge advances into the freestream velocity while the leading edge encounters the flow when yawing right. This is from the perspective of being behind the rotor into the freestream with counter-clockwise rotation. Another possible explanation is the sting mount producing a wake that only the downstream rotor encounters.
Fun facts:
Starting off this project I played with a number of "proof-of-concept" prototypes that were aimed at answering whether our proposed devise will work as assumed.
Proof-of-concept 1: Auto torque stabilization concept in a wind tunnel
Prototype 0.0 tested in iSSRL NCSU wind-tunnel shows dynamic stabilization
Prototype 0.1 tested in iSSRL NCSU wind-tunnel with a high speed camera with auto-tracking proved the dynamic stability. This shows that a contra-rotating dual rotor turbine can be dynamically stable under yawed operation!
Proof-of-concept 2: Mechanical power measurements in the water tunnel for a single rotor system.
The initial prototypes looked so ugly that I shiver to see them now. This was our 1st attempt to get into the water-tunnel to find the power output as a function of yaw angle for a 2 bladed rotor (RC hobby prop.).
Proof-of-concept 3: Auto torque stabilization concept in a wind tunnel
Proof-of-concept 4: Tethered underwater model with inertial instrumentation.
- Arduino Nano
- BNO 055 inertial sensor
- Micro SD card - onboard data recording
- Battery pack